Welcome
Center for Information Technologies - CIT
Center for Information Technologies
RP - RAPID PROTOTYPING
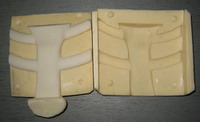
Artificial breastbone made by RP device at CIT
Manufacturing of the sternum or breastbone (a long flat bone located in the center of the human chest) by RP technique that was implanted into human body by medical surgeons in Kragujevac Clinical Center.
Artificial breastbone made by RP device at CIT is produced of medical materials. It was done in scope of joint cooperation of CIT and Faculty of Medicine, Kragujevac and Faculty of Mechanical Engineering, University of Nis. The procedure saved life of a patient who was operated. It is the first such a case of practical application of RP technologies in area of medicine in Serbia. Medical material used for this implant is not expensive and is also used in dental medicine with unlimited lifetime.
RP device (ZCorporation ZPrinter) that was used for production of this breastbone implant is situated in CIT. Device was used only for manufacturing prototypes of machine parts and auto parts, until this implant. For medical purposes, prototypes of femur and tibia bones were made at CIT, for exercises of students at Faculty of Medicine, Kragujevac, in scope of regular Faculty education process.
Press links
daily newspaper Vecernje Novosti
MONDO

What is rapid prototyping?
Rapid prototyping is the most common name given to a host of related technologies that are used to fabricate physical objects directly from CAD data sources. Today's additive technologies offer advantages in many applications compared to classical subtractive fabrication methods such as milling or turning:
Objects can be formed with any geometric complexity or intricacy without the need for elaborate machine setup or final assembly;
Rapid prototyping systems reduce the construction of complex objects to a manageable, straightforward, and relatively fast process.
Application
This has resulted in their wide use by engineers as a way to reduce time to market in manufacturing, to better understand and communicate product designs, and to make rapid tooling to manufacture those products. Surgeons, architects, artists and individuals from many other disciplines also routinely use the technology.
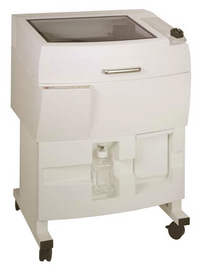
Devices for Rapid prototyping located in CIT
CIT is equipped with high-tech rapid prototyping system, ZCorporation ZPrinter 310 RP System based on 3D printing technology. This system is capable of producing prototypes with dimensions up to 200x200x250 mm. Even the most complex parts are made within couple of hours, and smaller parts within minutes. Applications of such prototypes are numerous, from design verification, through functional testing, to unique capability of pouring metal directly in moulds produced with this system. It can provide virtual and real 3D GIS models as well as rapid prototyping, rapid tooling and reengineering of devices for use in hydro-informatics systems.
Roland MDX-20, which is a combination of CNC mill and CMM digitizer, is also at the CIT’s premises. It can produce parts as large as 203.2x152.4x60 mm with accuracy up to 0.025 mm, and digitizing parts of same size with accuracy of 0.05 mm. The materials for use with this system are: plaster, modeller wax, polystyrene, aluminium, brass, etc
A laser 3D scanner Roland PICZA LPX-250 is capable of digitizing objects up to 254 mm in diameter and 406.4 mm in height. The scanning process is fully automated, and can be made in rotary and planar mode. Scanning resolution is 0.2 mm in planar mode.
A manual CMM device, Immersion Microscribe G2LX, is located at the CIT. This model is capable of digitizing objects that are within the reach of mechanical arm, and that reach is 1.67 m wide, with resolution of 0.3 mm. The use of this device is manual, and it is compatible with most of CAD and 3D modelling software available today.
Roland LPX-250
Immersion Microscribe
Roland MDX-20
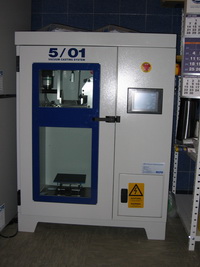
VACUUM CASTING MACHINE
for producing fast multiple prototype parts in Nylon PA6, PU based Vacuum Resins Epoxies and Wax. Maximum Mould Size (HxWxD) is 530 x 450 x 425 mm.
Most recent developments include Vacuum Cast glass filled Nylon, producing components that exhibit properties far in excess of other rapid prototyping technologies. All of this is possible without hard steel tooling and the associated lead times and costs. The process involves encasing a master model in Silicone rubber, a vacuum is then applied to the mould, following this the mould is cured in a oven at around 70°C – usually overnight. Once cured the mould can be cut open, at which point the master model is removed leaving a mould cavity perfectly replicating the master model. Master models can come from a range of sources, the most common being Stereolithography models, but the increasing range of CAD driven 3D printers are also a useful source. The quality of the master model dictates part quality and complexity can be accommodated through multi segment moulds.
Once the mould is complete the mould segments are put back together, secured and placed in the bottom compartment of the machine. The two components PU materials are then weighed, the pigment added and placed in the automatic mixing robot in the top of the machine.
At this point the PLC takes over the process to vacuum cast the component and once this is complete the casting is cured at 70°C. Following this the mould segments can be separated and the part removed. All that remains is for the part to be trimmed and polished as required.
Everything from industrial components, consumer products, lenses and small batch production can be achieved using the Vacuum Casting process. Typically between 30 and 50 colour matched parts can be produced from a single mould with first off parts available within two to three days.
Typical applications include:
High quality prototypes for product design verification
Small batch production for bespoke products
Functional Nylon components in a range of grades – particularly good for living hinges and high strength
Automotive ‘hot test’ and specialist manufacture
High quality wax masters for investment casting
Production of EP tooling resin moulds
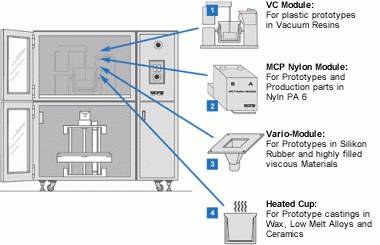
High-tech rapid prototyping system
ZCorporation ZPrinter 310 RP System based on 3D printing technology. This system is capable of producing prototypes with dimensions up to 200x200x250 mm. Even the most complex parts are made within couple of hours, and smaller parts within minutes. Applications of such prototypes are numerous, from design verification, through functional testing, to unique capability of pouring metal directly in moulds produced with this system. It can provide virtual and real 3D GIS models as well as rapid prototyping, rapid tooling and reengineering of devices for use in hydro-informatics systems.
Activities of the Center
Research and development in the area of information technologies, engineering software and designing
and implementation of computer operated systems, especially in area of information systems building
and hydroinformatics.
Educational activities
Organizing of educational activities in the spheres of information technologies, engineering software and
designing and implementation of computer operated systems. Publication activities (printed materials,
electronic multimedia releases - CD, DVD, internet and eLearning contents).
Cooperation
Research conducted at the
University of Kragujevac in collaboration with world renowned institutions such as: M.I.T., the Technical
University of Athens, the Imperial College, Harvard University, the Hong Kong Polytechnic University,
Nanyang Technological University Singapore, and in conjunction with domestic and foreign industry.
Address: S.Janjic 6,
34000 Kragujevac, Serbia
Tel/Fax: +381 34 304710
E-mail: gruja@kg.ac.rs